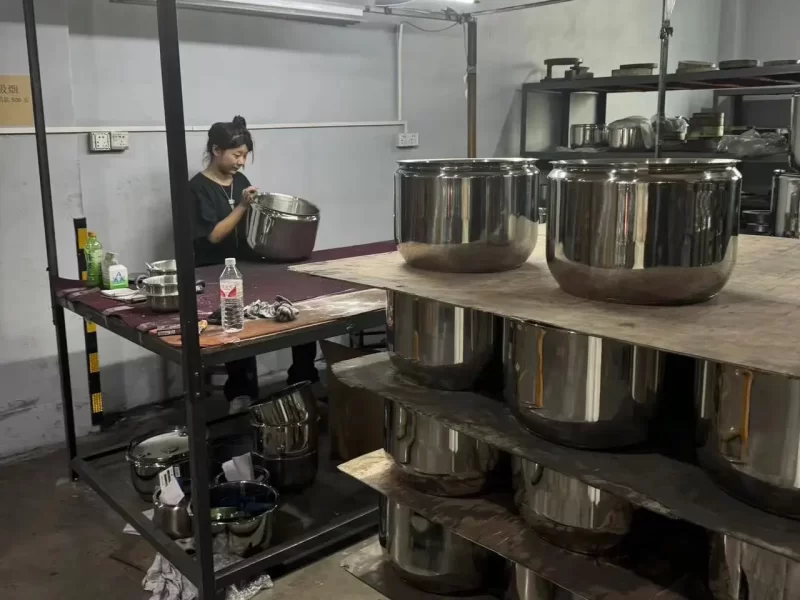
Our pressure cookers are set with 6 layers of safety protection. For example, the most typical U-shaped pressure cooker is equipped with a safety handle, a pressure limiting valve, an anti-blocking cover, a springย relief valve, an alarm valve and a pressure relief window.ย As a stainless steel pressure cooker manufacturer, safety assurance is the top priority factor of the pressure cookerย series. The most effective process to ensure safety is through quality tests.ย Therefore, we have a specialized department for quality testing. From the raw materials to the assembly line, each step goes through strict quality control to ensure safety and reliability. The steps of quality inspection are as follows.
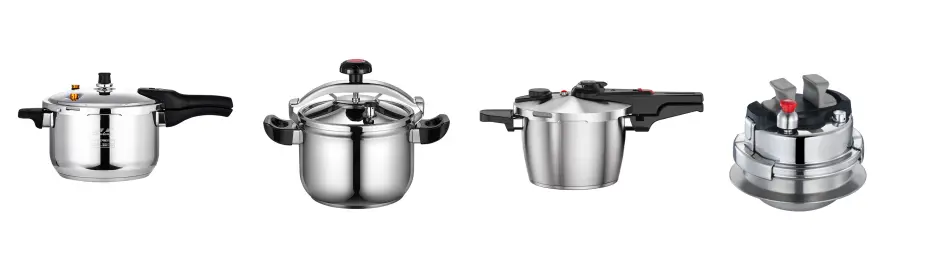
Inspection of raw materials for pressure cookers
The raw materials of pressure cookers include stainless steel materials and accessories such as sealing rings and safety valves. Linkton pressure cooker factory will test the composition, mechanical properties and high-temperature resistance of these materials before starting manufacturing.
Stainless steel material composition analysis
Use X-ray fluorescence spectrometer (XRF) to analyze the chemical composition of stainless steel materials to ensure that the materials contain the correct ratio of chromium and nickel, such as 304 stainless steel should contain at least 18% chromium and 8% nickel.
Mechanical properties test
Perform a tensile test (Tensile Testing) and use a universal material testing machine to measure the tensile strength, yield strength, elongation and other indicators of the material.
Seal and accessories inspection
Analyze the chemical composition of the seal ring to ensure that it does not contain harmful substances, and use a high-temperature and high-pressure steam box to test its temperature resistance, and test its acid and alkali resistance under a high-acid and alkalinity instrument to ensure that it can still maintain good sealing in different environments.
Pressure cooker component test
From the inside to the outside of the pressure cooker, each component is carefully inspected.
Dimension and shape verification
Use a high-precision electronic vernier caliper to measure the size, and use a three-dimensional coordinate measuring machine (CMM) to check whether the shape conforms to the design drawing.
Welding point inspection
Use magnetic particle testing (MT) or penetrant testing (PT) methods to check whether the welding point has defects such as cracks and holes.
Sealing and functional testing
Apply standard pressure on the pressure test bench to observe whether the pressure relief valve is working properly, and check whether the pot cover is completely sealed and leak-free.
Pressure cooker assembly quality test
The assembly quality mainly checks the tightness and sealing of the assembly parts, as well as the practical performance of the pot cover. During the assembly process, each worker must ensure that the quality of all parts meets the requirements
Tightness and sealing
Use a torque wrench to test the tightening torque of the screws to ensure that the specified tightness is achieved; use a pressure test device to test the sealing of the connection between the lid and the pot body.
Rotation and locking mechanism
Manually operate the lid to open and close, ensuring that it rotates smoothly and the locking mechanism is reliable.
Pressure cooker functional test
Pressure test
Place the pressure cooker in the test environment, heat it to the set pressure value (for example, 1.5 atmospheres), and check whether the pot body is deformed or leaking after some time.
Safety function test
Test whether the pressure relief valve can open automatically under overpressure conditions, and whether the safety locking mechanism prevents the opening operation under pressure.
Overheat protection
Simulate overheating conditions, use a temperature sensor to monitor the temperature change in the pot, and ensure that the overheat protection device can cut off the heating source in time.
Pressure cooker performance test
In our testing center, we simulate the environment of home and commercial kitchens and conduct a series of functional and performance tests on the pressure cooker product series
Cooking Performance
Use standard ingredients to conduct cooking experiments, record heating time and food cookedness, and ensure that heat distribution is even and cooking time is reasonable.
Durability Test
Simulate daily use in a laboratory environment and conduct a certain number of opening and closing cycle tests to evaluate the durability of the product.
Cleaning and Maintenance
After cleaning the pressure cooker, perform functional tests again to ensure that the cleaning process does not affect its normal use.
Pressure cooker appearance test
To ensure the appearance quality of the product, we conduct a strict inspection of the surface of the pressure cooker. Observe the surface smoothness of the pot body and lid to ensure that there are no scratches, bubbles or other defects, and verify the corrosion resistance of the stainless steel surface through corrosion testing. At the same time, we also check the labels and markings on the product to ensure that they are clearly visible and contain necessary instructions and safety warnings.
Packaging and transportation test
During the packaging stage, we use appropriate packaging materials to protect the product from damage during transportation, and verify the effectiveness of the packaging through vibration and drop tests that simulate the transportation environment. Each product must be equipped with necessary accessories and instructions. Finally, we conduct random sampling inspections to ensure that each product in the production batch meets the quality standards.
Documentation and reports
We keep records of all tests and inspections, including detailed data from raw material inspection, component inspection, assembly quality, functional testing, etc. Finally, a detailed quality inspection report is summarized to record the problems found and their solutions to continuously improve product quality.
Quality inspection process throughout each production link
In order to ensure product quality, Linkton pressure cooker manufacturers have set up a strict quality control system in each production link. From raw material procurement to warehousing, pre-production preparation, processing stage, assembly stage, to finished product inspection and comprehensive inspection before delivery, each step is carefully monitored and tested. Through real-time monitoring, intermediate product inspection, assembly process supervision, and functional and appearance testing of finished products, it is ensured that each pressure cooker meets high standards of quality requirements.
Conclusion
The production safety of stainless steel pressure cookers is of vital importance to manufacturers. From the selection of materials to the final inspection process, each step is strictly monitored to ensure that the finished product is safe and reliable. If you want wholesale and custom pressure cookers, you can believe that our stainless steel pressure cookers are produced with great attention to safety.