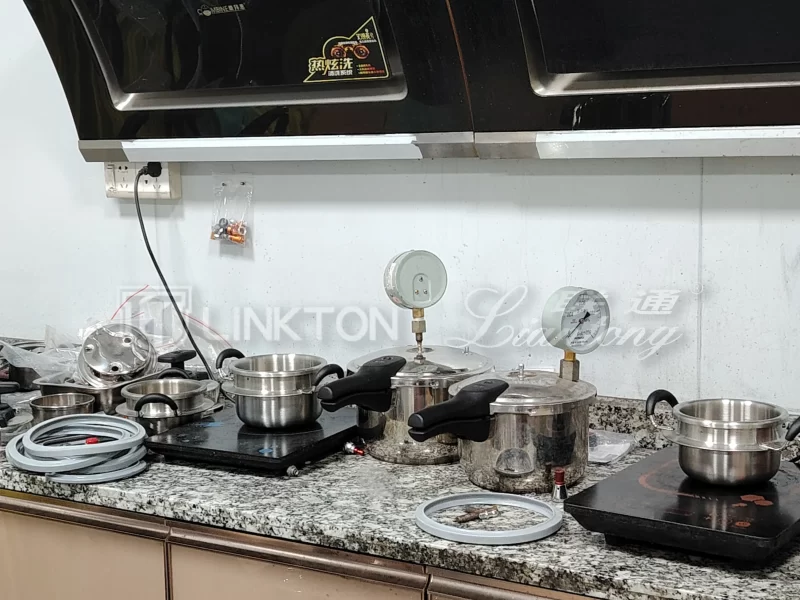
The pressure cooker safety is of vital importance, which involves consumer safety and risk protection for merchants. Therefore, it is the basic responsibility of pressure cooker manufacturers to conduct strict safety tests before the product leaves the factory. Linkton pressure cooker manufacturer adhere to the production principle of safety and quality first and strictly implement product quality standards. This article will introduce how to conduct pressure cooker safety tests before the cooker leaves the factory.
Key Safety Testing Procedures and Methods
Pressure Testing
Pressure testing is a core aspect of pressure cooker safety inspection. We use automated pressure testing equipment to place the pressure cooker under specific conditions and gradually increase the pressure to the maximum limit. During the test, the equipment monitors the stress and pressure changes of the pressure cooker in real time to ensure that no rupture or leakage occurs under extreme pressure. In addition, we perform multiple pressurization and release cycles to confirm the long-term safety of the pressure cooker.
Material Inspection
The quality of stainless steel directly affects the durability and safety of the pressure cooker. We perform material composition analysis using X-ray fluorescence (XRF) to ensure that key elements like chromium and nickel meet international standards. We also conduct tensile and impact tests to verify the materialโs strength and resilience under high-temperature and high-pressure conditions.
Seal Integrity Check
The seal of the pressure cooker is critical to safely maintain pressure. We use an airtightness tester to pressurize the seal of the pressure cooker and immerse it in acidic or oily water for 72 hours to check for bubbles to ensure its quality.
Safety of Operating Components
The operating parts of the pressure cooker, such as valves, handles, and safety locks, must work properly under pressure. We have safety valve testing equipment, as well as functional tests that simulate user operations, such as repeatedly opening and closing valves, measuring the load-bearing capacity of handles, and testing safety locks to ensure that they can quickly lock and release under pressure, providing additional safety.
Durability Testing
The durability test simulates the long-term use conditions and home or commercial environment of the pressure cooker, conducts heating and cooling cycle tests, and checks for deformation, cracking or seal failure, to verify the structural stability of the pressure cooker and ensure that the pressure cooker maintains good performance over a long period.
Technical Standards for Ensuring Pressure Cooker Quality
To ensure the quality and safety of our pressure cookers, we strictly adhere to international standards, such as ISO 9001 Quality Management System certification. Additionally, we follow various industry standards for testing and improvement, ensuring our products are competitive in global markets.
Linkton Safety Pressure Cooker Manufacturer
As a professional stainless steel pressure cookers manufacturer, we have over 30 years of experience producing high-quality kitchenware for global markets. We are equipped with advanced production equipment and technology and have a team of experienced R&D and testing professionals dedicated to providing our customers with the safest and most reliable products.
Conclusion
The safety of a pressure cooker directly impacts the userโs experience and the protection of life and property. As a manufacturer, we commit to ensuring that every pressure cooker leaving our factory has undergone rigorous safety testing to meet the highest standards. In the future, we will continue to uphold our quality-first and safety-focused philosophy, providing safer and more reliable products to users worldwide.